Economical Efficiency
Saving time, labor-hours and building material cost are the things real estate customers are increasingly demanding from their builders, contractors and developers. UDK wall blocks play an important part in the economy and speed essential to economical and profitable construction projects.
UDK
8 blocks/m2
height: 200 mm
length: 600 mm
brick
128 pcs/m2
height: 65 mm
length: 250 mm
UDK wall blocks have larger sizes, are precise in dimensions and weigh remarkably little compared to traditional building materials.
They have hand grips and tongue and groove joints which make them easier to use and lay.
The diagram on the bottom shows clearly that apart from the fact that considerably fewer blocks are required for 1 m2 of wall, a worker can lay a certain number of high-speed building bricks a day and just as many UDK blocks and therefore build a much greater area of wall. Construction crews can complete their work faster saving time and money.
Since walls built with UDK wall blocks together with UDK TBM© will be built much faster, following works such as installation of floors and roofs, as well as plastering, infrastructure (electric cables, water pipes) installations and partitioning will start and progress faster, saving labour and time.
UDK wall blocks are 3 to 4 times lighter than the equivalent volume of traditional construction materials (approximately 75% lighter than concrete) which means transport capacity is maximized and freight cost reduced. Below is a comparison of building material transported on a 20 ton truck:
Ttruck Load (20 tons) | Aerated Concrete Blocks | Shell Stone Blocks | Silicate Bricks |
Wall Size | 96 m2 | 32.5 m2 | 34 m2 |
Wall Thickness | 375 mm | 400 mm | 380 mm |
Product Volume | 36 m3 | 13 m3 | 13 m3 |
The cost of 1 m2 wall built with UDK wall bolcks will be less than walls built with other materials:
Comparative price for 1 m2 | Aerated Concrete Blocks | Shell Stone Blocks | Silicate Bricks | Ceramic Bricks |
Cost Wall Material, % | 58 | 51 | 80 | 77,8 |
Cost of Mortar, % | 2,3 | 9,5 | 9,3 | 12 |
Cost of Labor, % | 16,5 | 21,4 | 24 | 28,7 |
Insulation Cost, % | 0 | 47,5 | 47,5 | 47,5 |
Internal Plaster, % | 6,7 | 9,3 | 8,5 | 8,5 |
External Plaster, % | 16,5 | 16,5 | 16,5 | 16,5 |
Total Cost, % | 100 | 155 | 186 | 191 |
Productivity per Shift (8 hours) | 15 m2 | 7,4 m2 | 7,4 m2 | 7,4 m2 |
All cost calculations in % is based on average prices of popular building materials.
High Strengts
Autoclaved aerated concrete has high thermal insulation properties. 375-400 mm walls built with AAC blocks do not require additional insulation. UDK wall blocks are solid, robust and can safely be used in load bearing walls.
During manufacture autoclaved aerated concrete is steam-cured in a pressurized autoclave (190°С, 12 Bar). The concrete actually turns to rock, forming microscopic crystals of calcium silicate hydrate. It is the analogue of natural stone mineral that gives to AAC its high strength.
UDK Gazbeton AAC blocks are divided into Classes by Strengts B2,0 and B2,5 which is confirmed by Conformity and Test Certificates.
UDK AAC blocks can be applied for construction of load bearing walls of private houses with several floors as well as for construction of non-bearing and bearing walls of high-rise framehouses with no limitation to the number of floors.
Light Weight
Density is one of the main technical characteristics of autoclaved aerated concrete. Density (ρ, kg/m3) is the weight of 1m3 of dry material. 60% of AAC is a porous mass (air porosity). For example, AAC with density D500 (average density kg/m3) is 75% a porous mass. AAC with density D400 has an even higher porosity.
Due to low density, the weight of AAC wall is three times less than the weight of a respective brick wall and 1,7 times less than the weight of ceramsite concrete wall.
In terms of volume, one UDK GAZBETON block can replace 10 bricks and can be installed at one laying, which makes building speed faster and saves labor. AAC blocks have hand grips, which is very convenient. Tongue and groove also makes quality laying of blocks very easy even for inexperienced builders. The light weight of UDK wall blocks means less weight and less pressure on the structure and foundations of a building which means proportional saving along the line: shipment-building-use of building. This makes UDK blocks ideal for use in multi-story buildings as well as in building private homes.
Here are the savings you get while using light-weight UDK wall blocks:
- Save on shipment of blocks to the building object (a truck can take a larger volume of the product);
Truck (20 tons) | AAC Blocks | Shell Limestone | Silicate Bricks |
Wall Size | 96 m2 | 32,5 m2 | 34 m2 |
Wall Thickness | 375 mm | 400 mm | 380 mm |
Volume of Product | 36 m3 | 13 m3 | 13 m3 |
- Lower weight of 1 m2 of walls and partitions leads to lower weight of the building as a whole, which consequently lowers load on the foundation;
- Good thermal insulation of frame structure leads to savings on heating each 1 m2 of the building.
Thermal Insulation
Buildings constructed with UDK wall blocks will be warmer in winter and cooler in summer.
High thermal insulation is one of the determining characteristics of autoclaved aerated concrete. Its cellular structure gives it a thermal insulation characteristic several times higher than that of concrete and сlay or silicate bricks.
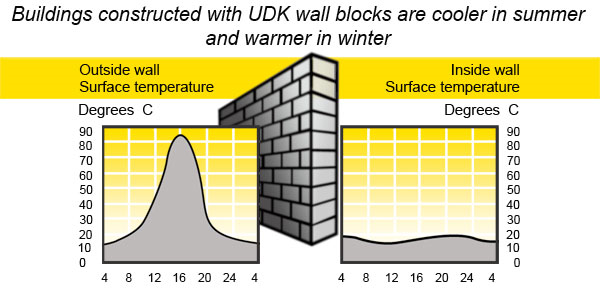
A wall built with UDK wall blocks and UDK TBM© thin bed mortar provides solid insulation without thermal bridging associated with most conventional brick and mortar walls. By using UDK TBM© additional savings are made on laying blocks, heating and cooling, and additional insulation materials are not needed.
Thermal Conductivity Comparison |
Wall Type (W/m K) | UDK Block 400 0,10 | Shell Limestone 0,58 | Silicate Brick 0,87 | Ceramic Brick 0,81 |
In summer, the exterior of buildings are subject to high fluctuations in temperature. In order to create cool, comfortable microclimate in buildings, tempertaure fluctuations inside buildings must be minimized. Thanks to effective combination of thermal insulation, thermal inertia and thermal mass characteristics, walls made with UDK wall blocks provide for minimum temperature fluctuations inside the building when the outside temperature fluctuates significantly.
Versatility
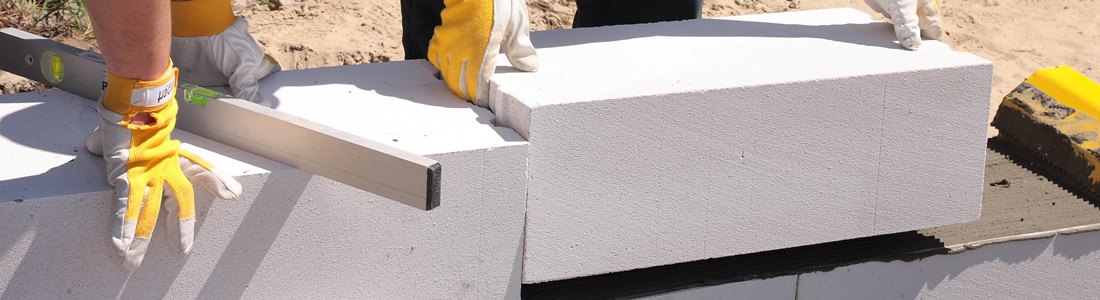
The high level of performance achieved by autoclaved aerated concrete means UDK blocks can be used in a variety of building applications:
UDK wall blocks are ideal for the constructing of all types of external and internal walls in a most economical way, whether load bearing, solid or self-supporting walls. Significant savings in cost and time are possible by using 375 or 400 mm thickness UDK wall blocks in a single row without additional insulation.
UDK wall blocks are a tried and tested, fast and efficient way of constructing external single row solid walls. They are produced in most economical sizes to suit the builder’s requirements
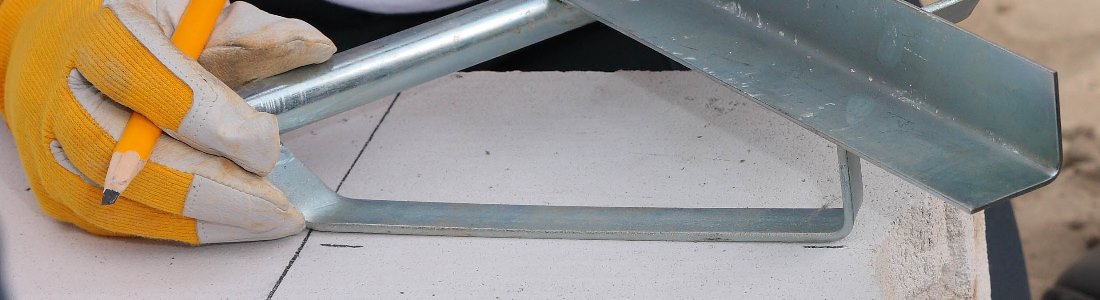
UDK blocks can be used for the construction of the inner rows of two or three row cavity walls in combination with a brick external row, with ventilation or thermal insulation material.
Quallity control ensures high precision of dimensions of UDK wall blocks. It allows to build faster and save building materials. Due to minimal tolerances (±1 mm) of blocks, building with UDK wall blocks is economic, precise and fast.
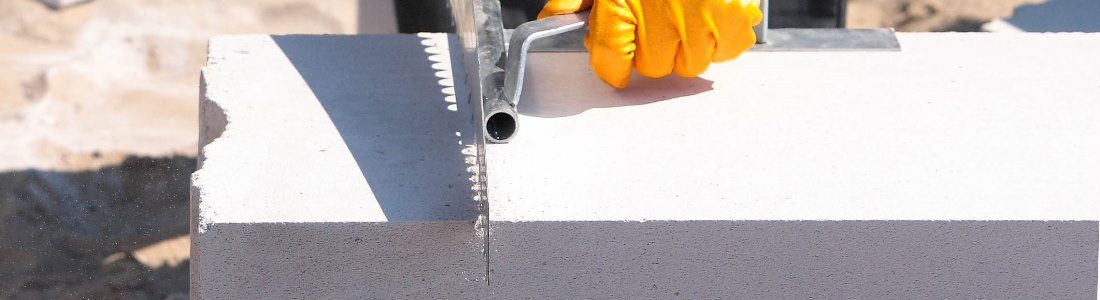
UDK wall blocks can be easily shaped. AAC is can be sawed, drilled and filed with the help of an ordinary hand instrument. Blocks of necessary shape can be used for constructing walls, partitions, fencing of balconies, fireplaces, ladders and even for construction of various architectural elements. For rigidity of construction it is better to use blocks with tongue and groove. Large-sized blocks have grips for easy mounting.
Fire Resistance
UDK wall blocks are non-combustible, will prevent the spread of fire, endure high temperatures over long periods of time and can be used in buildings requiring all classes of fire resistance.
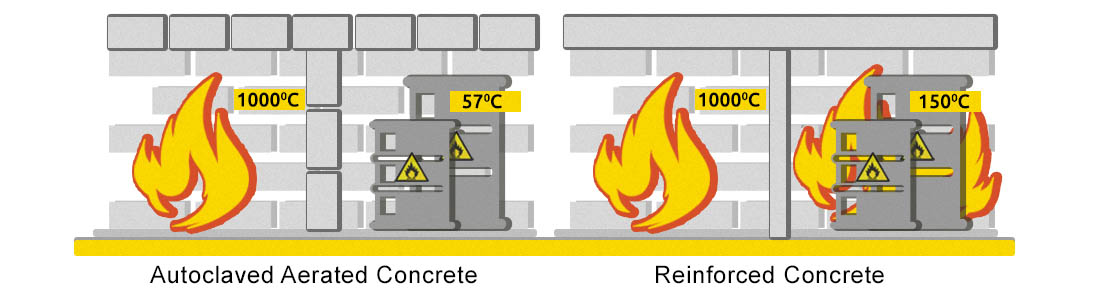
Fire separation walls built with UDK wall blocks are:
- Noncombustible;
- Will limit temperature rise on the unexposed side of a wall;
- Do not emit combustion gasses.
Walls built with UDK wall blocks do not transmit smoke and will contain fire. In case of afire, no poisoning gasses are releases.
AAC buildings have proven that even after a fire their walls did not collapse and only renovation of the finish were required to repair the impact of fire.
Seismic Design
Low density of UDK wall blocks in filler structures means less load on the foundation and building frame.
It in turn leads to lower material consumption and lower weight of the building.
Due to low density combined with high strength, buildings from AAC blocks have proved to have good earthquake resistance.
The table below compares post-earthquake data of a 16-storey building:
Building using AAC Blocks
External Walls (30 cm) |
720 m2 | 360 t |
Internal Walls(12,5 cm) |
680 m2 |
340 t |
Total | 1400 m2 |
700 t |
Horizontal seismic impact equals 40% of vertical load |
Horizontal Load |
700 t х 40% |
280 t |
Building using Bricks
External Walls (30 cm) |
720 m2 |
720 t |
Internal Walls (12,5 cm) |
680 m2 |
680 t |
Total |
1400 m2 |
1400 t |
Horizontal seismic impact equals 40% of vertical load |
Horizontal Load |
1400 t х 40% |
560 t |
This way, vertical load on building foundation of AAC walls is 360 tons less and horizontal load is 280 tons less.
Bearing capacity of the foundation increases and horizontal load on the building during seismic activity decreases.
Healthy Room Climate
Healthy room climate of a buildings has become vitally important nowadays. While designing a new building, we realize that any building should not only be functionally and aesthetically appealing, but also ecologically clean and environmentally friendly.
European Declaration on Environment pays great attention to building ecologically clean and healthy housing. Thus, viewing impact on the environment while applying AAC for building: raw material-production-application in building-use of building-recycling-utilization and storage, it can be characterized as ecologically clean material.
Another positive aspect is long term of use of buildings from AAC. This is the advantage of using building materials produced on the mineral basis.
Good thermal insulation qualities of AAC play a great role in maintaining energetic balance, warmth and clean air in the building. These component form microclimate that is so important for people’s health.
Comfort and Clean Air
Feeling of comfort is a very important criterion of microclimate. Comfort depends, first and foremost, on the temperature and humidity inside the building.
Low thermal conductivity of AAC makes temperature of internal surface of walls equal to air temperature inside the building, which results in temperature comfort. Temperature of wall surface can differ insubstantially from air temperature inside the building, which eliminates air drafts so typical for poorly insulated buildings.
UDK wall Blocks possess high vapor permeability, which makes process of drying faster and maintains heat and humidity comfort. Good air permeability of AAC helps create healthy and comfortable microclimate in the building.
UDK wall Blocks are resistant to rodents, insects and vermin. The walls will not decay with time.
Low Radioactivity
Low radioactivity is another important requirement to building materials.
According to radiation and hygienic assessment that estimates content of total natural radioactivity, UDK wall Blocks belong to the 1-st and highest class of building materials (according to standard ДБН В.1.4-1.01-97) and can be applied for all types of buildings without any restrictions.